Thermal Integration Guide
Overview
The Ouster lidar sensors offers an industry-leading combination of price, performance, reliability, size, weight, and power. It is designed for indoor/outdoor all-weather environments and a long operating lifetime.
The Ouster family of sensors consist of three models, the OS0, OS1, and OS2, with differing beam configuration and vertical resolution, but identical mechanical dimensions.
The contents of this manual are applicable only to Rev 06 sensors. Please contact support@ouster.io with the sensor serial number to find out your sensor Rev information. For all other sensor hardware revisions, please refer to the respective hardware user manual.
Terminology
For the purposes of this document, let us first establish some common terminology that will be used in this guide.
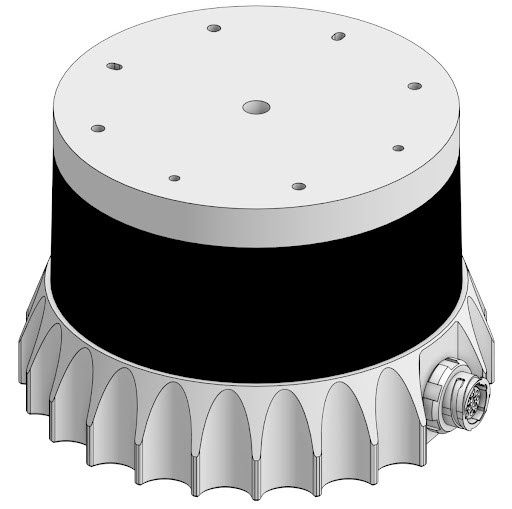
The Sensor without any heatsink or mounting plates
![]() Heatsink Base which doubles as the standard mounting plate. |
![]() Heatsink Radial is the radial finned heatsink modular cap. |
![]() Heatsink Halo The halo finned heatsink modular cap. Preferred when application needs to reduce sharp edges. |
![]() Heatsink Clamshell Is a reference heatsink for integrating into vehicles in locations that require tighter integration. |
![]() Heatsink Clamshell with an Ouster Sensor. |
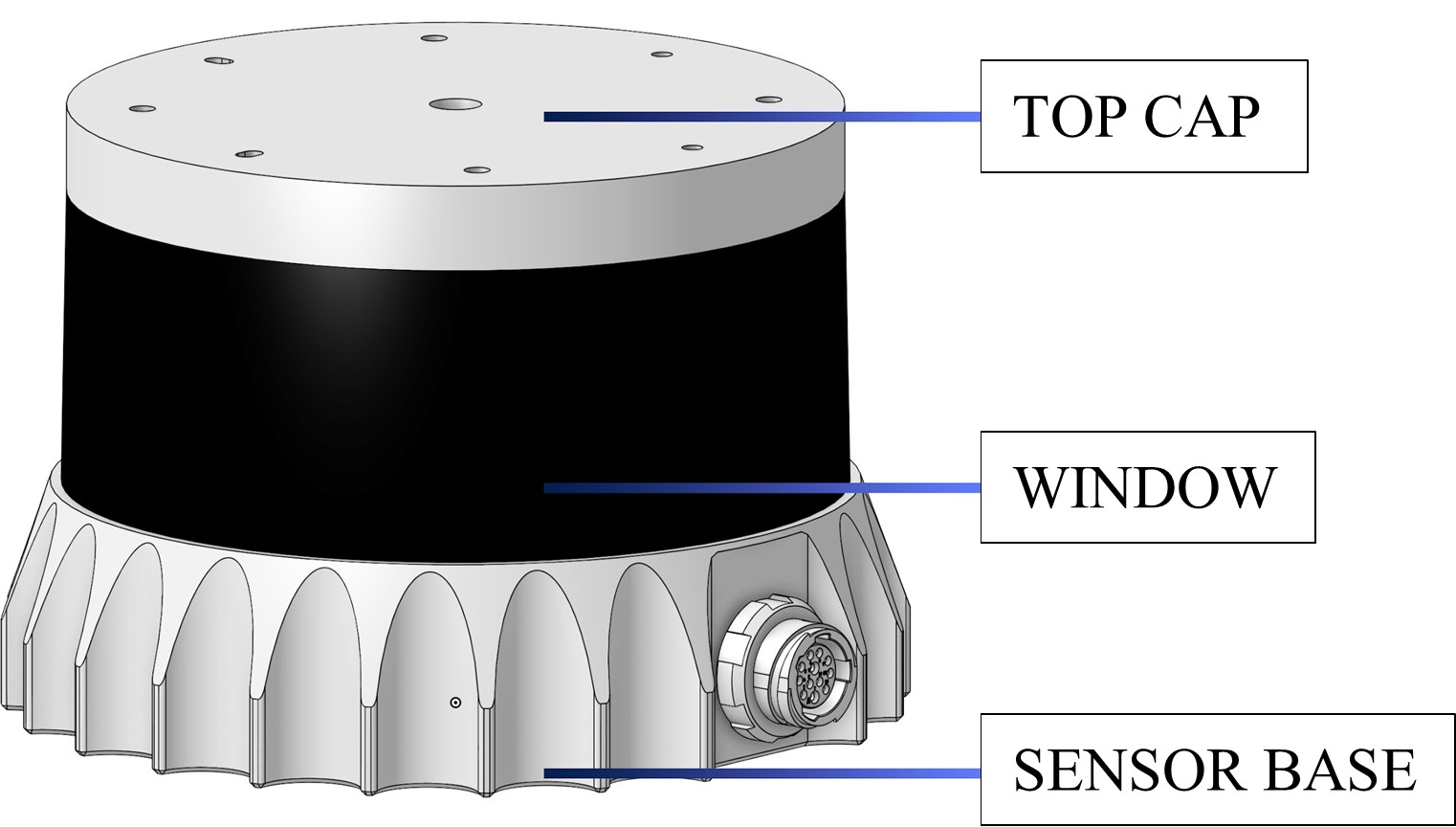
Top Cap, Window and Sensor Base
Top Cap The top of the sensor, which accepts modular heatsinks such as the Heatsink-Radial, Heatsink-Halo and has mounting features for seamless integrations.
Window The window through which the lasers are emitted.
Sensor Base The base of the sensor which has the connector mounted to it.
Free Convection The movement caused within a fluid by the tendency of hotter and therefore less denser material to rise, and colder, denser material to sink under the influence of gravity, which consequently results in transfer of heat. |
Stagnant Air Air that is not moving other than by Free Convection. |
Forced Convection The transfer of heat due to the bulk movement of fluid molecules over an object. The bulk movement can be due to wind, fan, vehicle motion, etc. |
For the following reference tests in the Thermotron SE-1000-6-6 Environmental Chamber, our FORCED CONVECTION flow rate is 1000 cubic feet per minute (CFM). This is approximately 0.5 m/s or 1.8 km/h of air speed. The air in this chamber flows from top to bottom.
Performance Of Standard Design
Where does the heat come from?
There are two primary heat-dissipating assemblies in the sensor.
The Optical Turret - containing the lasers and receivers.
The Base Assembly - containing the computing, communication, and power.
The Optical Turret dissipates heat to both the TOP CAP
and the SENSOR BASE
. While, the BASE ASSEMBLY
conducts most of its heat to the SENSOR BASE
.
It is important in any sensor mounting integration design to accept heat from both the TOP CAP
and SENSOR BASE
.
Another important heat source factor to consider is the Sun. If the sensor will be operating in full sun you will need to account for the solar load (~1000 W/m2). In our testing, solar load reduces the maximum operating temperature by approximately 8ºC.
Please see the Sunshade Concept Design for inspiration on possible solutions.
Where does the heat go?
Standard Heatsinks
The sensor comes with two standard heatsinks attached to it.
The base heatsink and mounting plate. (referred to as HEATSINK-BASE)
The radial finned or halo heatsink modular caps. (referred to as HEATSINK-RADIAL, HEATSINK-HALO)
Note
Both have the same thermal performance.
It is also possible to create your own custom heatsinks for your specific integration, given that it adequately dissipates the heat from the sensor. For more information contact our Support team.
In the reference test conducted in the thermal chamber under FORCED CONVECTION (0.5 m/s) with the standard heatsinks, 38% of the heat is conducted into the HEATSINK-BASE.
While the remaining 62% of the heat convects to the air through the HEATSINK-RADIAL, SENSOR BASE, and WINDOW. Refer to Forced Convection With Standard Heatsink Heat Path.
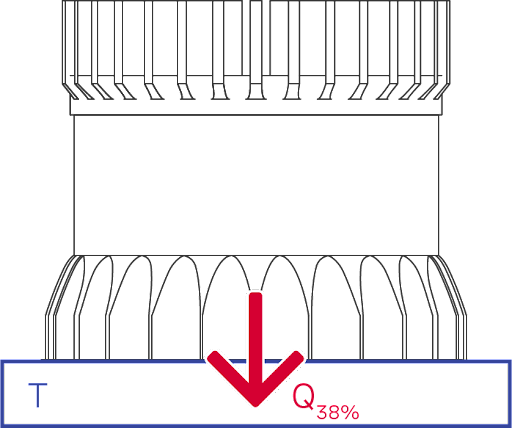
Forced Convection With Standard Heatsink Heat Path
Similarly, for FREE CONVECTION (Stagnant Air) in the thermal chamber with the standard heatsinks, 45% of the heat is conducted into the HEATSINK-BASE.
While the remaining 55% of the heat convects to the air through the HEATSINK-RADIAL, SENSOR BASE, and WINDOW. Refer to Stagnant Air with standard heatsink heat path.
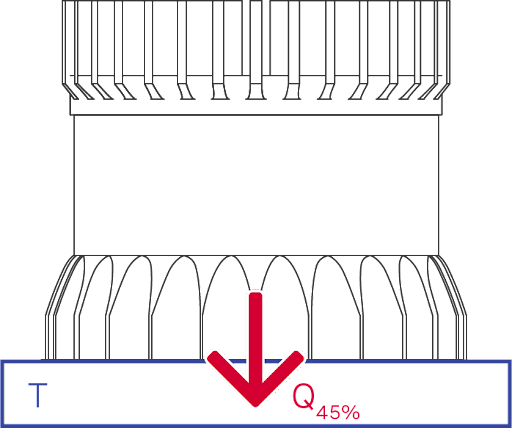
Stagnant Air with standard heatsink heat path
Clamshell heatsink
The clamshell design was created to give you a reference of an integrated installation where heat dissipation is accomplished primarily through conduction into a vehicle chassis.
In the reference test conducted in the thermal chamber under FREE CONVECTION (Stagnant Air) with the clamshell heatsink, 87% of the heat is conducted into the HEATSINK-CLAMSHELL. While the remaining 13% of the heat convects to the air through the HEATSINK-CLAMSHELL, SENSOR BASE and WINDOW. Refer to Clamshell Heat Path.
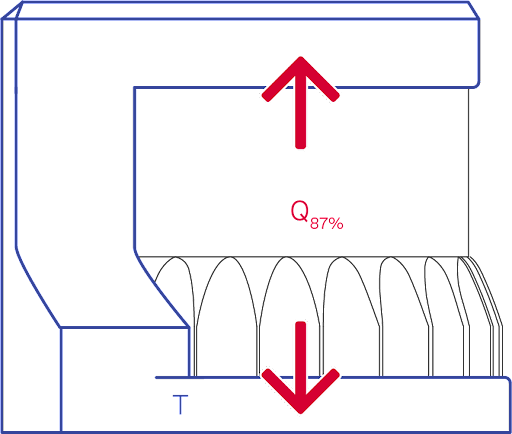
Clamshell Heat Path
Now that you have a good understanding of where the heat goes, we will discuss some best practices when designing your own heatsinks and integrations.
Thermal Integration Best Practices
There are a few considerations when designing your heatsink integrations for your application.
1- Choose a material that has a high thermal conductivity to ensure the heat is efficiently conducted away from the sensor.
If possible, the sensor should not share an interface with materials with low thermal conductivities. Materials such as wood (~0.12 W/m-K), glass (~0.935 W/m-K), and rubber (~0.140 W/m-K) have low thermal conductivities. In general, Aluminum alloys are best both for their thermal conductivity and mass properties.
Below is a list of recommended Aluminum alloys and their thermal conductivities:
2- Ensure that all interfaces are clean and free from debris. Debris and contaminants can reduce the thermal conductivity at an interface.
3- Torque bolts appropriately for the mount material and bolts specified. This will ensure the best thermal conductivity at an interface without damaging the threads. Below is a list of torque values for the sensor by screw size:
2 N-m: M3-0.5 mm
HEATSINK-BASE to SENSOR BASE
HEATSINK-RADIAL or -HALO to sensor TOP CAP
4 N-m: M4-0.7 mm
HEATSINK-CLAMSHELL top to clamshell riser
7 N-m: M6-0.8 mm
HEATSINK-CLAMSHELL base to sensor TOP CAP
HEATSINK-CLAMSHELL base to clamshell riser
4- Use Thermal Interface Material (TIM) for any irregular or non machined surfaces. TIM usually comes in a paste or pad form; it works to increase the surface area that heat can be conducted through at an interface.
5- Ensure that the sensor is not over constrained if mounting to both SENSOR BASE and TOP CAP. If the sensor is clamped between the surfaces that attach to the SENSOR BASE and TOP CAP, the WINDOW will experience deflection which will negatively affect the optical performance.
To ensure this does not occur we recommend using a TIM pad to ensure good conductivity while not over-constraining.
Ensure your implementation maintains the base and top of the sensor below the maximum chassis temperatures listed in Sensor Max Operating Temperature - Gen 1 OS1 with Legacy Cap.
To maximize FREE and FORCED CONVECTION, the area around the sensor should be unobstructed.
Design the shape of any heatsinks to maximize the surface area for FREE and FORCED CONVECTION while being thick enough to allow the heat to conduct through the material. Below are some recommended features:
![]() Air Flow Paths |
![]() Fins |
9- Whenever possible it is highly recommended to use heatsinks. For special integrations where the HEATSINK-RADIAL and HEATSINK-BASE are both removed, such as drone integrations, it is critical that the thermal alerts are monitored closely. For these types of integrations it is required to use the STANDBY
operating mode until adequate FORCED CONVECTION (e.g. from flying) is provided. Without heatsinks, if any thermal alerts are triggered, the sensor should immediately be put into STANDBY
mode or shut off until adequate heatsinking is provided.
Warning
If the sensor is consistently receiving thermal alerts due to the removal of the heatsinks, this will void the warranty.
Now that you have some best practices for your integration, we will discuss how to monitor your integration with Thermal Alerts.
Max Operating Temperatures
Max operating temperatures were calculated through reference tests conducted in Ouster’s thermal chambers. OS0, OS1, and OS2 are tested on HEATSINK-BASE is as shown below:
![]() OS0, OS1 Mounting Image |
![]() OS2 Mounting Image |
The results may vary slightly depending on test conditions such as air temperature, air flow, and sensor mounting.
Rev6 and Prior Sensors with FW v2.5.x
Max operating temperatures were calculated through reference tests conducted in Ouster’s thermal chambers. OS0, OS1, and OS2 are tested on HEATSINK-BASE is as shown below:
![]() OS0, OS1 Mounting Image |
![]() OS2 Mounting Image |
The results may vary slightly depending on test conditions such as air temperature, air flow, and sensor mounting.
Sensor Part Number |
Convective Air |
Stagnant Air |
|
---|---|---|---|
840-101xxx-03 (with Push-Pull Connector) |
Start of Shot Limiting Active (Performance 100% - 70%) |
Tchassis = 55ºC Tair = 50ºC |
Tchassis = 56ºC Tair = 40ºC |
840-101xxx-02 (with Locking Bayonet Connector) |
Max Temp Sensor Shutdown |
Tchassis = 65ºC Tair = 60ºC |
Tchassis = 60ºC Tair = 50ºC |
Sensor Part Number |
Description |
Convective Air |
Stagnant Air |
---|---|---|---|
840-102xxx-C |
Start of Shot Limiting Active (Performance 100% - 70%) |
Tchassis = 52ºC Tair = 47ºC |
Tchassis = 52ºC Tair = 37ºC |
840-102xxx-C |
Max Temp Sensor Shutdown |
Tchassis = 65ºC Tair = 60ºC |
Tchassis = 60ºC Tair = 45ºC |
Sensor Part Number |
Description |
Convective Air |
Stagnant Air |
---|---|---|---|
|
Start of Shot Limiting Active (Performance 100% - 70%) |
Tchassis = 58ºC Tair = 52ºC |
Tchassis = 52ºC Tair = 37ºC |
|
Max Temp Sensor Shutdown |
Tchassis = 65ºC Tair = 60ºC |
Tchassis = 65ºC Tair = 50ºC |
Note
Without a HEATSINK-BASE, thermal performance decreases by an estimated 4°C
Sensor Part Number |
Description |
Convective Air |
Stagnant Air |
---|---|---|---|
|
Start of Shot Limiting Active (Performance 100% - 70%) |
Tchassis = 62ºC Tair = 52ºC |
Tchassis = 62ºC Tair = 50ºC |
Sensor Part Number |
Description |
Convective Air |
Stagnant Air |
---|---|---|---|
|
Max Temp Sensor Shutdown |
Tchassis = 75ºC Tair = 62ºC |
Tchassis = 71ºC Tair = 60ºC |
Rev7 Sensors with FW v3.1.x
Sensor Part Number |
Description |
Convective Air |
Stagnant Air |
---|---|---|---|
860-10xxxx-07 OS-0/1 |
Start of Shot Limiting Active (Performance 100% - 70%) |
Tchassis = 63ºC Tair = 55ºC |
Tchassis = 63ºC Tair = 43ºC |
860-10xxxx-07 OS-0/1 |
Max Temp Sensor Shutdown |
Tchassis = 70ºC Tair = 62ºC |
Tchassis = 70ºC Tair = 52ºC |
860-10xxxx-07 OS-Dome |
Start of Shot Limiting Active (Performance 100% - 70%) |
Tchassis = 66ºC Tair = 56ºC |
Tchassis = 64ºC Tair = 44ºC |
860-10xxxx-07 OS-Dome |
Max Temp Sensor Shutdown |
Tchassis = 70ºC Tair = 60ºC |
Tchassis = 70ºC Tair = 50ºC |
Note
During Ouster’s testing process, we observed solar load reduces the maximum operating temperature by approximately 8ºC. Please refer to Sunshade Concept Design for inspiration on possible solutions.
Thermal Alerts
Shot Limiting - Sensors Running on Firmware v2.5.x and Prior
The sensor alert system and thermal management are designed to ensure safe and robust operation in demanding environments. As the environment temperature gets higher the sensor will selectively reduce the amount of power consumed to ensure continued operation in temperatures approaching the maximum listed in Sensor Max Operating Temperature - Gen 1 OS1 with Legacy Cap.
The sensor has four stages of operation related to high-temperature environments as shown in the High Temperature Operating Modes.
1- Normal Operation - This stage is the default when the temperatures are between the minimum and maximum specified in the datasheet.
In this stage, the sensor operates at full performance.
2- Shot Limiting Zone Entered - This stage is entered when the chassis temperature is within ~2ºC of the maximum specified temperature.
In this stage, the sensor continues to operate at full performance and produces an alert to notify you that the sensor may soon enter a reduced performance mode.
3- Shot Limiting Active - This stage is entered when the chassis temperature is at the maximum operating temperature listed in Sensor Max Operating Temperature - Gen 1 OS1 with Legacy Cap.
In this stage, the sensor continues to operate but at reduced performance. The number of shots will gradually decrease from 100% down to 50% until reaching the saturation temperature.
4- Shot Limiting Saturated - This stage is entered when the shots have been limited by 50%.
In this stage, the sensor will continue to limit the number of shots at 50% until the temperature rises approximately 5ºC.
5- Sensor Shutdown - This stage is entered when the chassis temperature reaches the sensor shutoff temperature listed in Sensor Max Operating Temperature - Gen 1 OS1 with Legacy Cap.
In this stage, the sensor will shut itself down to prevent damage.
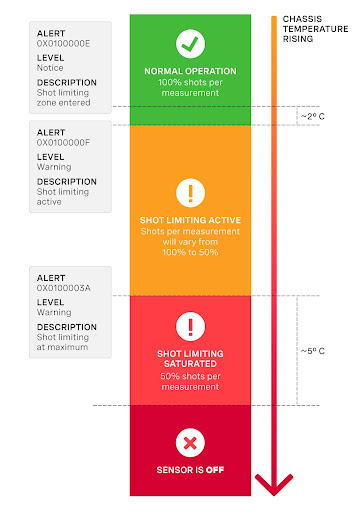
High Temperature Operating Modes
Note
50% shot limiting means 50% of the signal not 50% of the range.
Shot Limiting - Sensors Running on Firmware v3.x and later
Shot limiting is a process by which the Ouster sensor will automatically enter into state to safely prolong the operational performance of the sensor in high operating temperature conditions. There are several different levels of shot limiting that are described in the Shot Limiting Status Flags table.
The sensor has three operating states in order to manage high temperatures:
NORMAL (Status 0x00)
SHOT_LIMITING_IMMINENT (Status 0x01)
SHOT_LIMITING (Status 0x02 and greater)
In the NORMAL
state the sensor will perform to the range and precision specifications of the datasheet. When the sensor reaches a certain temperature, the sensor enters the SHOT_LIMITING_IMMINENT
state and issues alert 0x0100000E
which indicates shot-limiting will commence in 30 seconds. After 30 seconds have elapsed and the temperature remains elevated, the sensor issues alert 0x0100000F
and enters a SHOT_LIMITING
state.
In shot limiting state, the sensor reduces power to the lasers in order to reduce the thermal load. While in this state, sensor range and precision may degrade by up to 30%. The sensor will progressively increase shot limiting if the temperature remains elevated. If the sensor reaches its maximum degree of shot-limiting, it will throw alert 0x0100003A
.
If the sensor cools down while it is in either SHOT_LIMITING_IMMINENT
or SHOT_LIMITING
state, the sensor will return to the NORMAL
state.
An independent state machine runs for thermal shutdown. When the sensor reaches the maximum operating temperature specified in the table Maximum Thermal Performance, the sensor will enter a SHUTDOWN_IMMINENT
state and issue an alert in category OVERTEMP
. If the sensor temperature remains elevated after 30 seconds, the sensor will shut down and issue alert 0x0100006B
.
Note
Please refer to the Hardware User Manual to learn more about the maximum thermal performance.
Information regarding the shot limiting status is presented as part of the lidar data packet in the Configurable Data Packet Format. Shot limiting status will be a part of the packet header when config parameter udp_profile_lidar
is set to one of the following values shown below.
Single Data Return Format
Low Data Return Format
Dual Data Return Format
FUSA_RNG15_RFL8_NIR8_DUAL Return Format
The following flags are present in configurable data packet header:
Shot limiting status [4 bit unsigned int] - Indicates the shot limiting status of the sensor. Different codes indicates whether the sensor is in Normal Operation or in Shot limiting.
Shutdown Status [4 bit unsigned int] - Indicates whether thermal shutdown is imminent. This can be due to shot limiting being saturated, or due to any other over temperature conditions and depending upon the situation the appropriate alert is generated. When thermal shutdown is imminent, this flag will be set to 1 and the Thermal Shutdown Countdown field will be set to 30 seconds.
Shot limiting Countdown [8 bit unsigned int] - Countdown from 30 seconds to indicate when shot limiting is imminent. When the condition for entering shot limiting is met, the shot limiting status bit is set to 0x01 and the alert 0x0100000E takes effect. At this point the shot limiting counter will be set to 30 seconds and a countdown to initiate shot limiting will start.
Shutdown Countdown [8 bit unsigned int] - Countdown from 30 seconds to indicate that thermal shutdown is imminent. When a thermal shutdown is completed, the alert 0x0100006B will take effect and the sensor will automatically go to the ERROR state and stop outputting data.
The following table describes the codes in the shot limiting status flags, and what mode it corresponds to:
Shot Limiting status flags |
Description |
---|---|
|
Normal Operation. When the sensor is not in shot limiting, the shot limiting status flag will be set to 0x00, and shot limiting countdown will be set to 0x00. |
|
When the condition for entering Shot limiting is met, we set the Shot Limiting Status bit 0x01 and the alert 0x0100000E is in effect, informing that shot limiting is imminent. |
|
In this mode, we reduce the % of nominal laser duty cycle by 0-10% from NORMAL OPERATION. There will be an approximate reduction in the sensor max range by 3%. |
|
In this mode, we reduce the % of nominal laser duty cycle by 10-20% from NORMAL OPERATION. There will be an approximate reduction in the sensor max range by 6%. |
|
In this mode, we reduce the % of nominal laser duty cycle by 20-30% from NORMAL OPERATION. There will be an approximate reduction in the sensor max range by 9%. |
|
In this mode, we reduce the % of nominal laser duty cycle by 30-40% from NORMAL OPERATION. There will be an approximate reduction in the sensor max range by 12%. |
|
In this mode, we reduce the % of nominal laser duty cycle by 40-50% from NORMAL OPERATION. There will be an approximate reduction in the sensor max range by 16%. For OS2 and OSDome sensors this mode is when shot limiting is saturated and alert 0x0100003A is in effect. There will be an approximate reduction in the sensor max range by 21%. |
|
In this mode, we reduce the % of nominal laser duty cycle by 50-60% from NORMAL OPERATION. There will be an approximate reduction in the sensor max range by 21%. |
|
In this mode, we reduce the % of nominal laser duty cycle by 60-70% from NORMAL OPERATION. There will be an approximate reduction in the sensor max range by 25%. |
|
In this mode, we reduce the % of nominal laser duty cycle by 70-75% from NORMAL OPERATION. There will be an approximate reduction in the sensor max range by 27%. For OS0 and OS1 sensors this mode is when shot limiting is saturated and alert 0x0100003A is in effect. There will be an approximate reduction in the sensor max range by 27%. |
Appendix
Simple Thermal Model
Use the sensor CAD from the Downloads page to define the control volume
Simulate the sensor as a conductive material, such as aluminum, with a single power source.
Using the sensor product line data sheet to determine the power dissipated inside the control volume.
Note
The power dissipation varies during startup, nominal operation, and in cold ambient temperatures.
OS0/1 Detailed Thermal Model
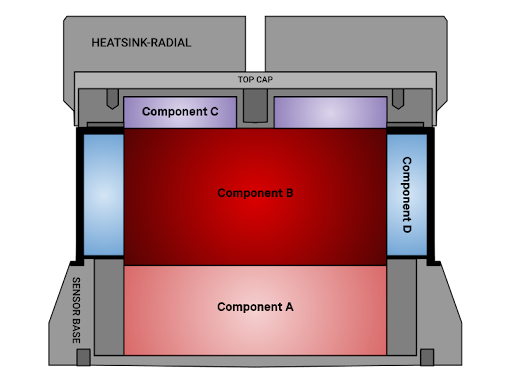
OS0/1 Thermal Model Cross Section
Thermal Model Specifications and OS0/1 Thermal Model Cross Section detail the specifications of the Thermal Model. Assumptions for Thermal Model are as follows:
Use case is to add the Thermal Model to CAD/simulation software to conduct CFD simulation.
Simulation is not transient, so thermal capacitance of materials and soak times do not need to be accurately estimated.
Simulation needs to estimate the power dissipation at the sensor’s three external components: HEATSINK-RADIAL, WINDOW, and SENSOR BASE enclosure given various external constraints.
Internal temperatures of the sensor do not need to be simulated.
Temperatures and heat fluxes need to be simulated at the control volume surface.
There is no contact resistance between components of the Thermal Model.
The Thermal Model assumes 18W power dissipation. This is a conservative assumption for a sensor at steady state conditions at higher temperatures. Sensor power draw is higher during startup and colder ambient conditions. Reference the relevant sensor datasheet for the power draw at startup and cold ambient temperatures.
Shape |
Material/ Conductivity |
Heat Dissipation |
|
---|---|---|---|
Simplified SENSOR BASE |
Cylindrical Bowl |
Aluminum 6061-T6 with clear anodize |
|
Simplified TOP CAP |
Cylindrical Bowl |
Aluminum 6061-T6 with clear anodize |
|
WINDOW |
Tube |
Polycarbonate |
|
Component A |
Cylinder |
2.68 W* m-1* K-1 |
6 W (at SENSOR BASE interface) |
Component B |
Cylinder |
Perfect conductor |
12 W |
Component C |
Tube / Donut |
0.401 W* m-1* K-1 |
|
Component D |
Tube / Donut |
0.209 W* m-1* K-1 |
Note
There is no contact resistance between components of the thermal model within the sensor control volume.
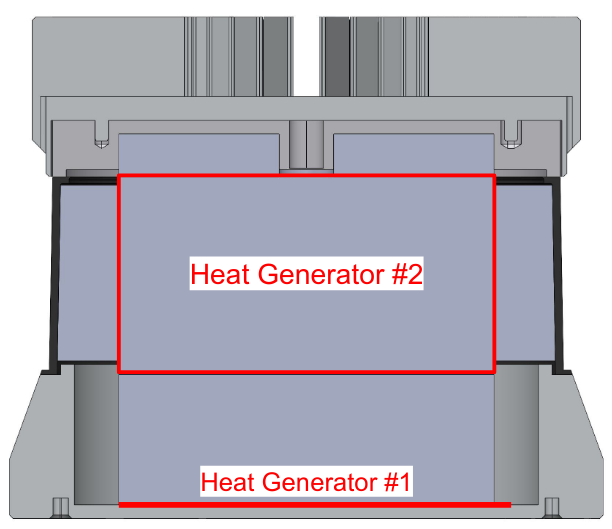
Thermal Model: Component Details
Component |
Surface or Volume |
Heat Dissipation |
|
---|---|---|---|
Heat Generator #1 |
Simplified Base Enclosure |
Top Surface |
6 W |
Heat Generator #2 |
Component B |
Whole Volume |
12 W |
Supplemental Thermal Load Cases
Tables below provides load cases for Rev7 OS0/1 at limited FOV, signal multiplier modes, and higher temperatures. The OS0/1 draws lower power at higher temperatures.
Note
The Ouster thermal team recommends using a simple 18 W total load as a conservative assumption even at higher temperatures when designing a sensor mounting hardware to simplify analysis and add margin to mounting hardware designs.
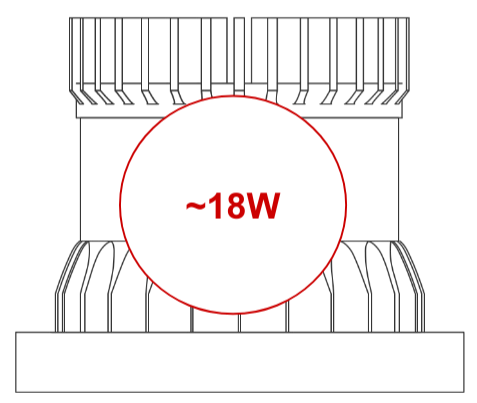
Thermal Load
FOV Signal |
Multiplier |
Total Power |
Heat Gen #2 |
Heat Gen #1 |
---|---|---|---|---|
360º |
1x |
18 W |
12 W |
6 W |
360º |
0.5x |
17 W |
11 W |
6 W |
360º |
0.25x |
16.5 W |
10.5 W |
6 W |
180º |
2x |
18 W |
12 W |
6 W |
180º |
1x |
17 W |
11 W |
6 W |
180º |
0.5x |
16.5 W |
10.5 W |
6 W |
180º |
0.25x |
16.25 W |
10.25 W |
6 W |
FOV Signal |
Multiplier |
Total Power |
Heat Gen #2 |
Heat Gen #1 |
---|---|---|---|---|
360º |
1x |
16 W |
10.7 W |
5.3 W |
360º |
0.5x |
15 W |
9.7 W |
5.3 W |
360º |
0.25x |
14.5 W |
9.2 W |
5.3 W |
180º |
2x |
16 W |
10.7 |
5.3 W |
180º |
1x |
15 W |
9.7 W |
5.3 W |
180º |
0.5x |
14.5 W |
9.2 W |
5.3 W |
180º |
0.25x |
14.25 W |
8.95 W |
5.3 W |
FOV Signal |
Multiplier |
Total Power |
Heat Gen #2 |
Heat Gen #1 |
---|---|---|---|---|
360º |
1x |
14.5 W |
9.2 W |
5.3 W |
360º |
0.5x |
14.5 W |
9.2 W |
5.3 W |
360º |
0.25x |
14.5 W |
9.2 W |
5.3 W |
180º |
2x |
14.25 W |
8.95 W |
5.3 W |
180º |
1x |
14.25 W |
8.95 W |
5.3 W |
180º |
0.5x |
14.25 W |
8.95 W |
5.3 W |
180º |
0.25x |
14.25 W |
8.95 W |
5.3 W |
Shot Limiting and Shutdown Plots (Rev7)
The following graphical representation shows expected shot limiting and shutdown limits based on the base enclosure bottom surface temperature and top cap (top) surface temperature. This data is only available for Rev7 sensors.
The measurement was taken with thermocouples placed at Top Cap Chassis and Base Heatsink Chassis as shown in the image below.
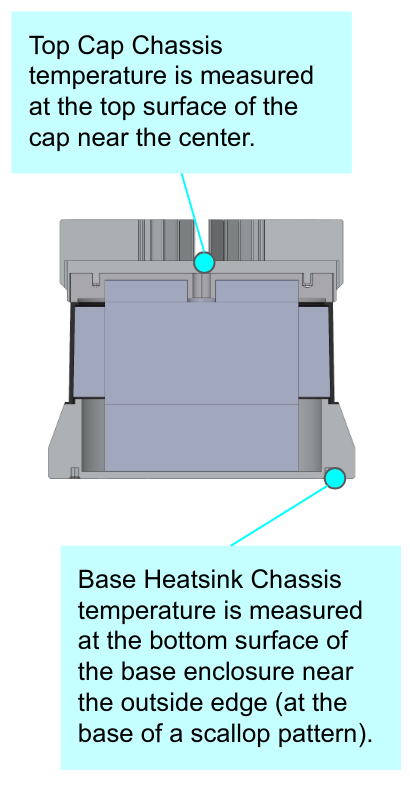
Thermocouple placement for measurement
Graphical representation: FOV= 360º and Signal Multiplier = 1
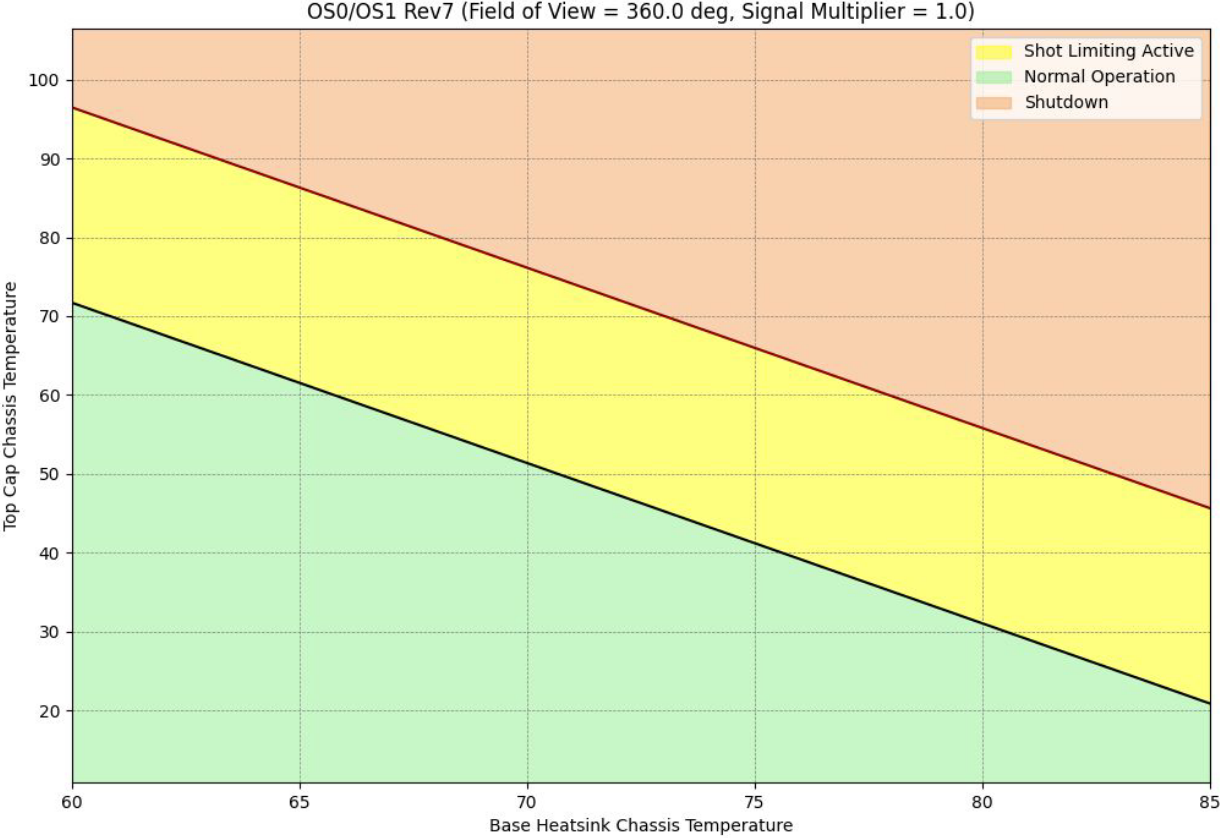
Field of View 360º, Signal Multiplier 1
Graphical representation: FOV= 360º and Signal Multiplier = 0.5
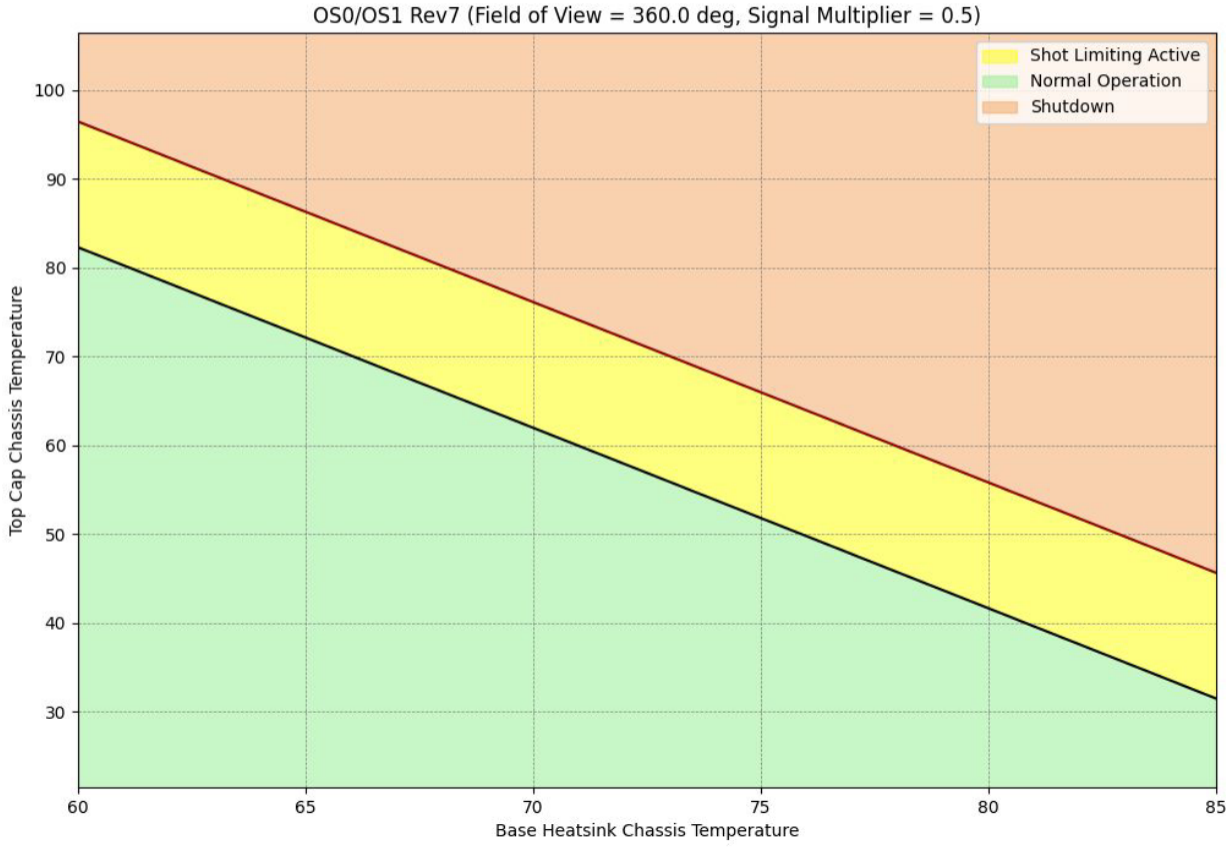
Field of View 360º, Signal Multiplier 0.5
Graphical representation: FOV= 360º and Signal Multiplier = 0.25
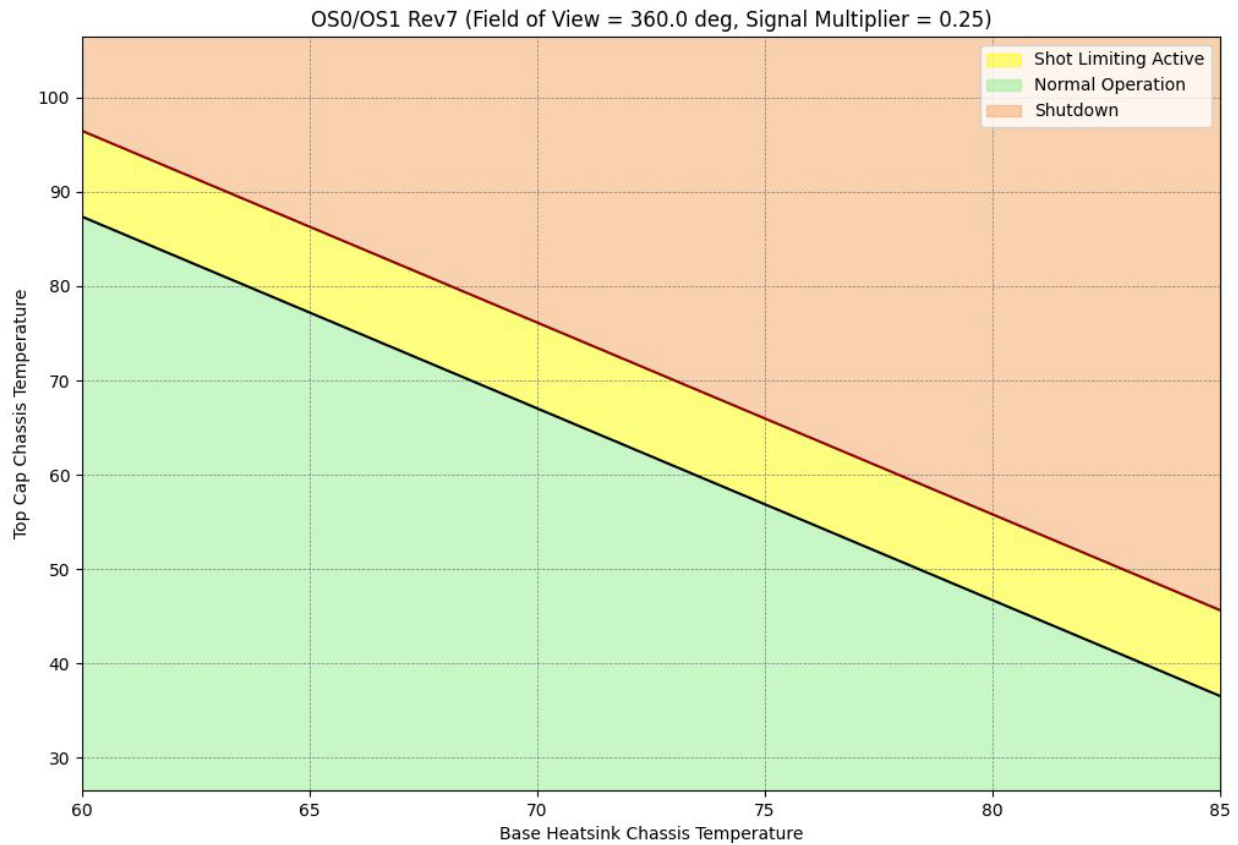
Field of View 360º, Signal Multiplier 0.25
Graphical representation: FOV= 180º and Signal Multiplier = 1
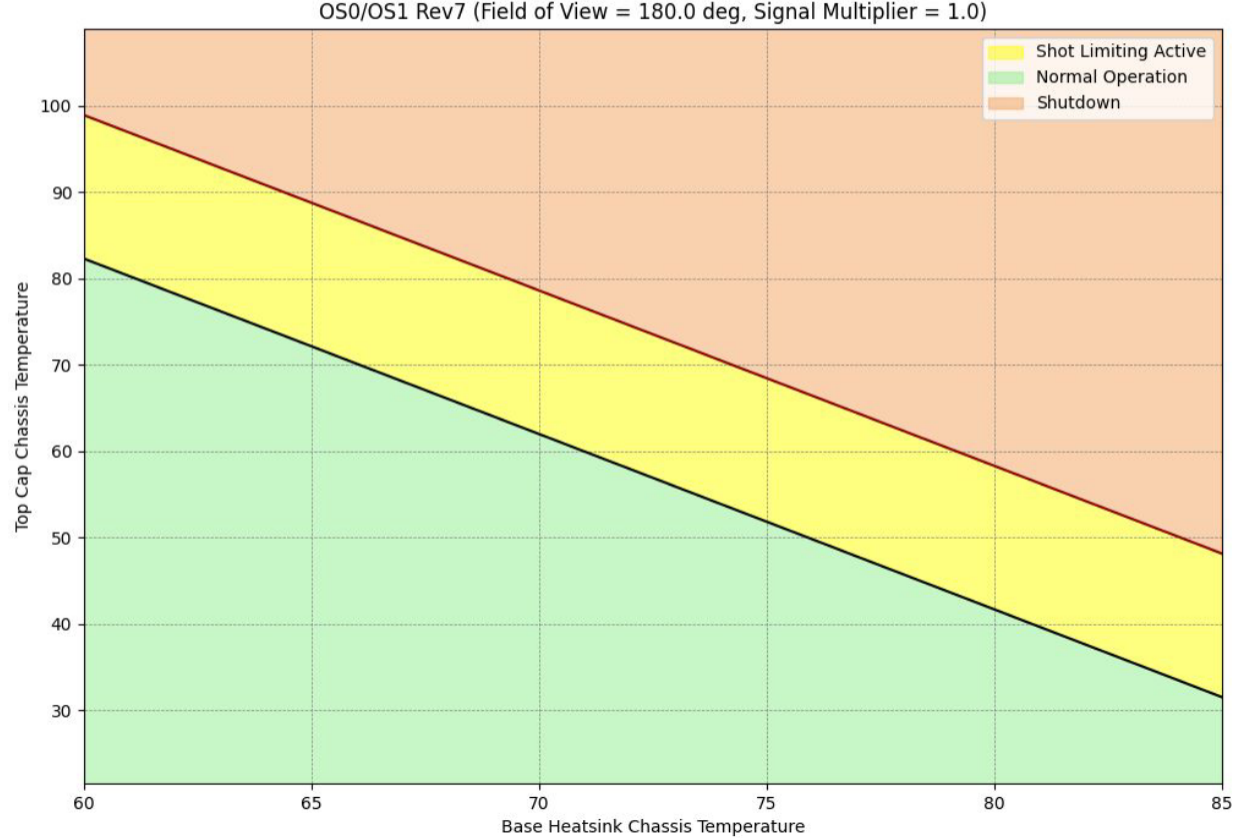
Field of View 180º, Signal Multiplier 1
Graphical representation: FOV= 180º and Signal Multiplier = 0.5
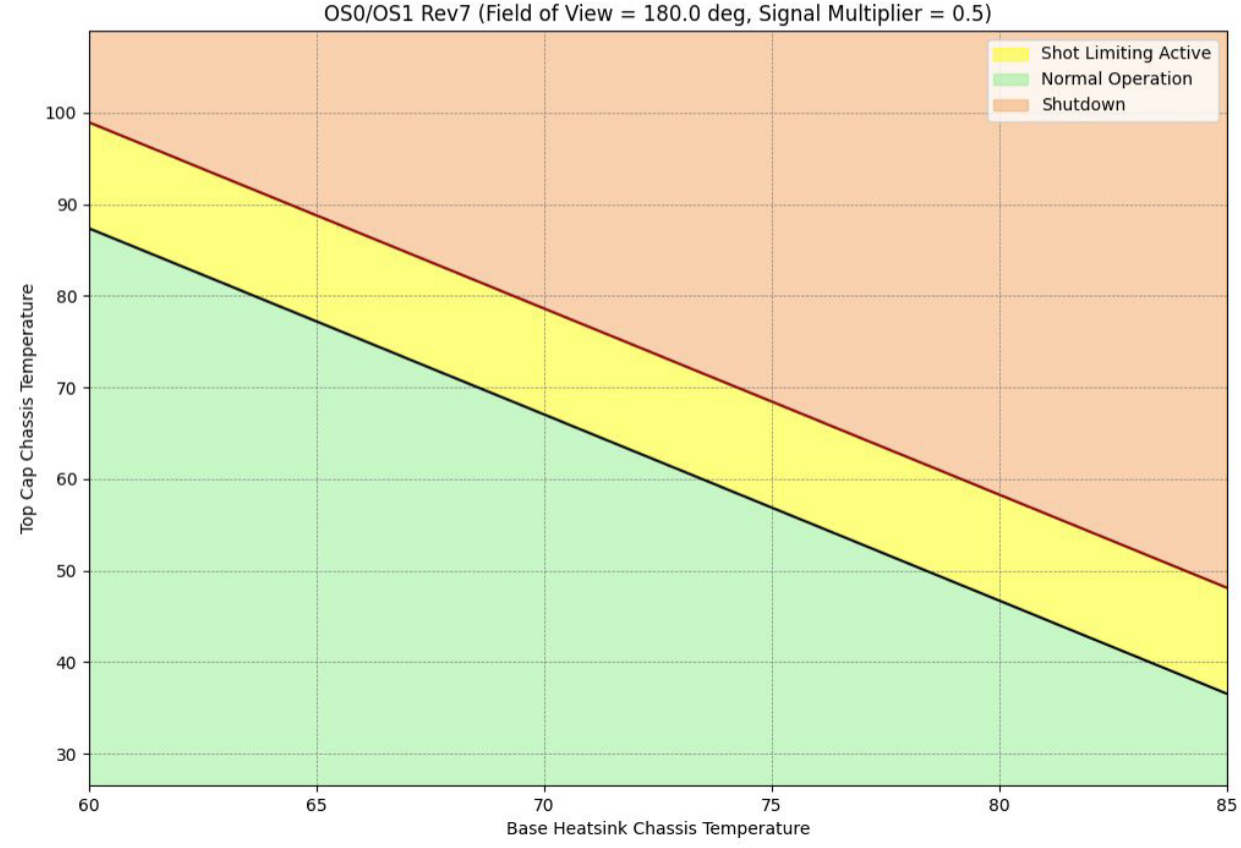
Field of View 180º, Signal Multiplier 0.5
Graphical representation: FOV= 180º and Signal Multiplier = 0.25
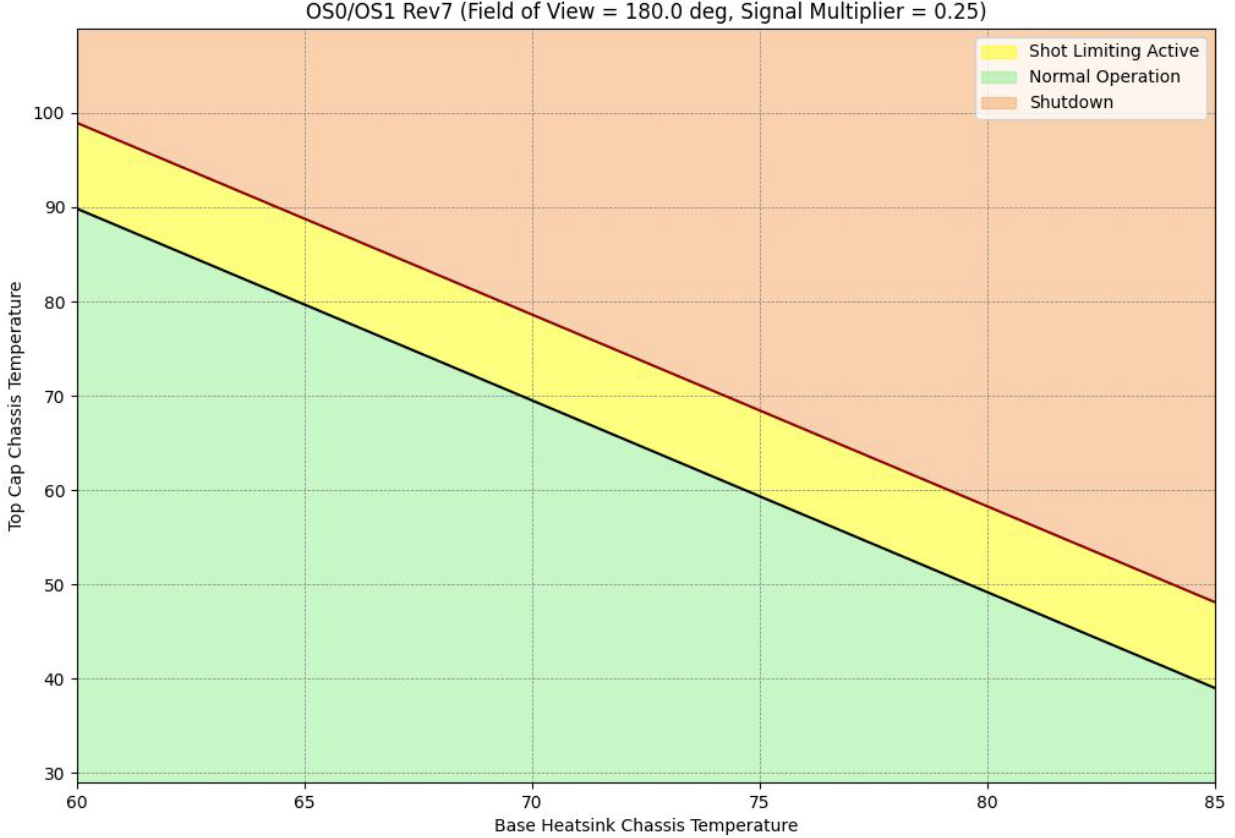
Field of View 180º, Signal Multiplier 0.25
Sunshade Concept Design
We have created a simple Sunshade Concept Design that may help mitigate the solar load. It attaches on top of the modular cap using the existing mounting holes in the modular cap.
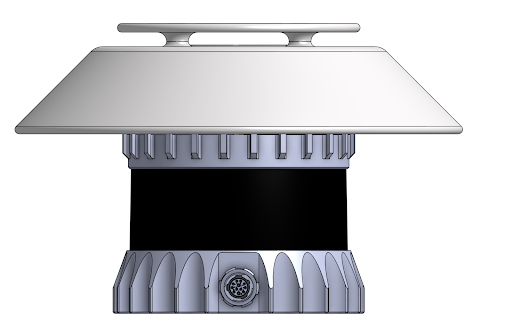
Sunshade Concept Design
Note
The modular cap (HEATSINK-RADIAL or -HALO) must remain attached to the TOP CAP of the sensor. The original M3-0.5x5 mm modular cap screws would need to be replaced with longer M3-0.5x30 mm standoffs.
This concept design is only for sensors with the modular cap that has the four mounting holes to interface with the TOP CAP.
840-101855-03 - Gen1 OS1 with Locking Bayonet Connector
840-102144-A/B/C/D/5/6/7 - Gen2 OS0 with Locking Bayonet Connector
840-102145-A/B/C/D/5/6/7 - Gen2 OS1 with Locking Bayonet Connector
This version is designed not to occlude any beams on a Gen2 OS1-128 with 45º VFOV. Design should be modified to accommodate wider VFOVs (90º) or more shade.
Warning
This design is meant to be an inspiration for your design and has not been validated.
The CAD model is available on Ouster Downloads page for you to iterate and fabricate.
Supported Products
The current firmware is supported on the following Ouster products:
Firmware 2.5.x
OS0, OS1, OS2:
GEN1: P/N 840-101-XXX-XX
Rev C: P/N 840-102-XXX-C
Rev D: P/N 840-102-XXX-D
Rev 05: P/N 840-102xxx-05
Rev 06: P/N 840-102xxx-06
Rev 7: P/N 860-10xxxx-07 (OS2 Only)
Firmware 3.1.x
OS0, OS1, OSDome:
Rev 7: P/N 860-10xxxx-07